EtherCAT Master: Features and Function
EtherCAT is a powerful real-time ETHERNET fieldbus system that has become standard in many industrial automation applications. With a software license, the 2nd generation controllers (750-821x/xxx-xxx), Touch Panels 600 (762-xxxx/8000-xxxx) or Edge controllers can run as an EtherCAT master.
The following functions are available:
- Distributed clocks
- Hot connect
- Bus diagnostics: In the configurator and with the PLC application
- Supported layer 7 protocols:
• CoE (CANopen / CAN over EtherCAT)
• FoE (File over EtherCAT)
• VoE (Vendor over EtherCAT)
The controller can be used as an EtherCAT master to control WAGO slaves with the EtherCAT fieldbus system (e.g., the EtherCAT Fieldbus Couplers 750-354 of the WAGO-I/O-SYSTEM 750). It is also possible to control field devices that are declared ine!COCKPIT via a standardized device description (see figure below).
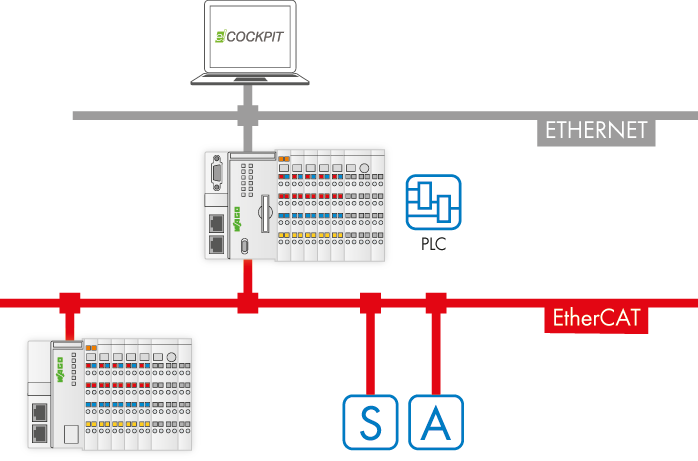
Besides the protocol stack in the form of a library, the EtherCAT Master software also provides the runtime system with components for direct access to the Ethernet interface and diagnostics. The EtherCAT system is configured using a special configuration dialog in the e!COCKPIT Engineering Software.
The following settings can be specified:
- Set controllers/touch panels as an EtherCAT master
- Select field devices to be addressed
- Define the topology of the network
- Set parameter values to be sent to the slaves upon startup
Note
Note the required settings for using the EtherCAT master!
Note the following settings. Correct operation of the EtherCAT master on the controller is not possible without these settings:
• Disconnect the Ethernet ports and enable Port X2 for EtherCAT (see Disconnect Ethernet Ports and Enable EtherCAT Port).
• You must disable the Broadcast Protection function in the controller. Otherwise, the EtherCAT master functionality cannot be used (see Disable Broadcast Protection Function).